How is the timber flooring dried to achieve moisture content at factory?
The suitable moisture of the floor is very important to get against the bowing, size changing during using. The moisture control of engineered wood flooring is actually happening in each process during the production.
1. The Timber Veneer Moisture:
1.1Air Dry (AD)
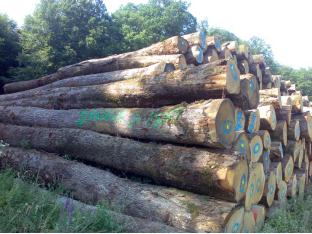
We never use flesh wood, all the logs we are using should be kept in stock for at least 6 month to 1 year period after it being harvest. This process we call it “Timber Air Dry“, The longer this period is, The more inner stress in the wood is released.
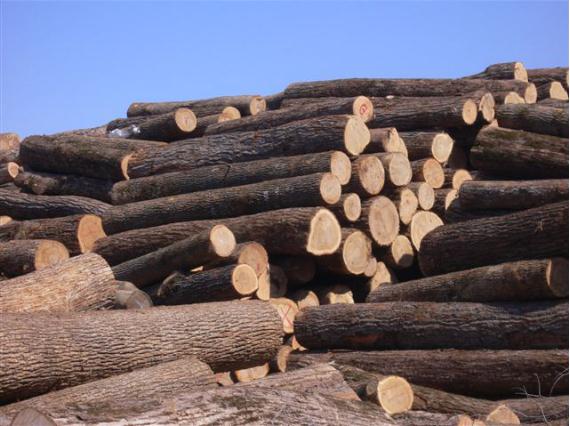
LOG STOCK IN AIR DRY
So when log was cut into timber it is about 30-40%. while the surface moisture has gone to a point which we call: “saturated moisture” In this point, the most moisture surround cells has mostly gone.
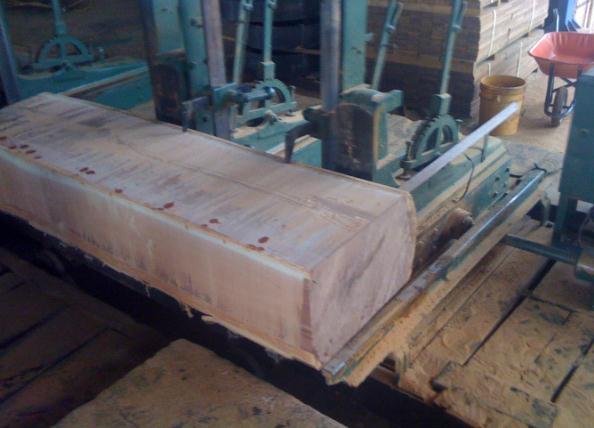
1.2. Kiln Dry
After the log being cut into wood cubic or timber boards, we have 2 ways to get veneers, and the moisture control process is also different due different way of veneering.
1.2a.
We dry the one inch (about 25-28mm) rough timber in the kiln dry facility for 4-8 weeks. the target is to dry to timber into 8-12% moisture (according to different wood species.) to get rid of the moisture in the cell. In this step, The facility temperature has to be well controlled step by step and being monitored.
Some species need several times steamed spray to use the steam to help the water get out of wood gently. Avoid the wood cracking when water get out.
Timbers before Drying
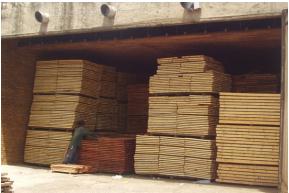
Timbers after drying and sanding

After this process, we will take the Kiln dried timber to frame saw to cut into lamellas: 2mm-3mm-4mm-6mm.
Frame Saw Process
1.2b.
For the long and wide planks, or for some species, we are mostly using the another way by cutting the veneer first before Kiln Dry.
In this way, We use bandsaw to cut the rough AD timber into rough veneers. E.g: In order to get final veneer size 4mm, sometimes we have to saw 6.5-7mm veneers, because it is still wet.
After the bandsaw process, We will do a “Second time Air Dry” for the “wet veneers”. We will rack and separate the veneers by steel rack and put them like the way below:
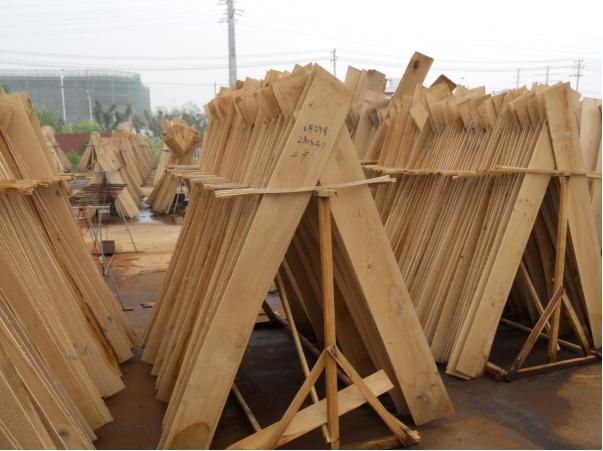
This could take about 1 week to 10 days time.
- In order to get rid more of the inner stress of the wood.
- To get the more of the moisture out surround the cells.
After the “second time AD”, We will still have to put the veneers into “Kiln dry Facility”. Since the veneer is thinner then timber, this process only takes 1-2 weeks then the veneer will get to 6-10% moisture content.
After we get the KD veneers, we will do the sanding/size reform, then we will use the plastic film to warp those veneers for stocking.
2. The plywood moisture control:
The plywood are made by thin rotary veneers (1mm-2mm) which need to be dried in 4 steps:

2.1 Log Air Dry
Same as the timber for veneers, the timber for plywood also need proper air dry for several month to get inner stress released after harvest.
2.2 Oven Dry
Since the rotary veneers are thin, and mostly from softer wood species, we have a 40 meter oven dryer with high temperature roller inside. This process takes 15 minutes to get the veneers to be dried at MC: 8+-2%.
2.3 Hot Press
When the veneers are glued to each other and being hot pressed, the moisture will be again being changed to a low level 6-8%. During this process, the different part of plywood moisture will be not quite stable, thus we going to the final part:
2.4 Moisture Balance Kiln Facility
The moisture balance facility is similar like the Kiln dry facility but much lower temperature (around 30-40 degree centigrade). And it will help to get each part of the plywood moisture be even.

Plywood in the moisture balance facility
After this process, we will do sanding, size forming the plywood and stock them for production purpose.
3. The preparation during flooring production
As most of the top layer timber veneers and plywood are pre-stocked to get quick production and delivery for flooring production. So before we glue and press the veneers+plywood, we will get both of them into moisture balance facility again.
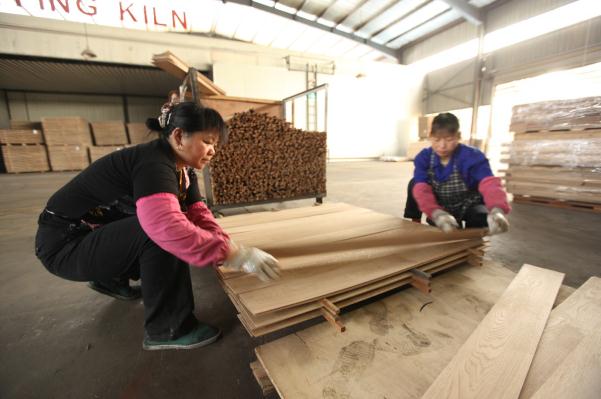
Workers are racking veneers to get into kiln facility to do moisture balance
There are two purpose of this process:
- Some stocked veneers moisture are not even. Some part of wood are 7%, some part of the wood are 10%, which is not good for flooring forming. This process will get the all the veneers within very small difference of MC, e.g: 7+-1%
- Because Engineered flooring are being glued by two different parts. The stress of two parts are all different and during the using, the moisture absorb rate also vary from species to species. We have a very serious formula that the veneer and plywood moisture has to be different before it glued together to avoid future problems. For example, For 15/4mm Engineered Oak Flooring with 4mm Oak + 11mm Eucalyptus plywood. When the Oak veneer moisture is about 7%, the plywood moisture need to be 9%. This is a key thing to keep the floor straight. This is vary according to different species and different weather condition for using the floors. For example, For the North European market, we are doing the finished flooring MC into 6-8% only. But for South East Asia countries, we are doing it about 9-11%., For Australia market, we are mostly control the moisture at about 8-10%. But for Perth, we are doing it more wet than in other part of Australia.
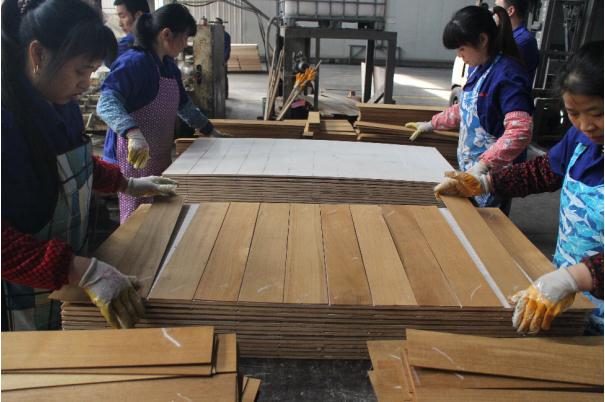
Veneer + Plywood Gluing ready for cold press
With our many years’ experience, those figures are the safest condition for engineered floors to get straight. And being stable in different weather and air moisture conditions in most part of the world.
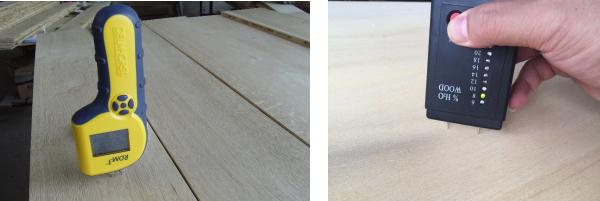